法蘭制造流程
合金管件制造工藝說明
材料:不銹鋼
交期:標(biāo)準(zhǔn)產(chǎn)品常年現(xiàn)貨
描述:聯(lián)系站長免費領(lǐng)取相關(guān)標(biāo)準(zhǔn)及重量表
規(guī)格: DN20-DN3000
在線咨詢 交期:標(biāo)準(zhǔn)產(chǎn)品常年現(xiàn)貨
描述:聯(lián)系站長免費領(lǐng)取相關(guān)標(biāo)準(zhǔn)及重量表
規(guī)格: DN20-DN3000
-
一、制造工藝說明
1.P91管件制造工藝流程
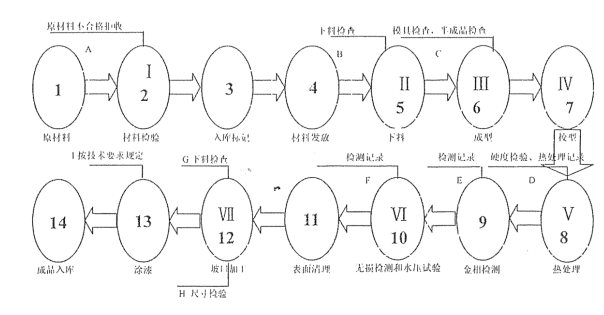
注:Ⅰ、Ⅱ、Ⅲ、Ⅳ、Ⅴ、Ⅵ、Ⅶ為控制環(huán)節(jié)
A、B、C、D、E、F、G、H、I為控制點
1、2、3、4、5、6、7、8、9、10、11、12、13、14為工序號
2、過程控制
2.1材料復(fù)檢
2.1.1我公司擁有多臺材料及成品檢測用專業(yè)檢測設(shè)備,對于新進廠的材料依據(jù)相應(yīng)標(biāo)準(zhǔn)進行以下復(fù)檢。
1)光譜儀進行材料光譜分析;
2)測厚儀測量管材、板材壁厚;
3)卡尺和盒尺測量管材的外徑及端口圓度偏差;
4)目測管材(逐件進行)的外觀無凹坑、裂紋、結(jié)疤、重皮、應(yīng)光滑無氧化皮等缺陷;外觀應(yīng)符合有關(guān)標(biāo)準(zhǔn)的要求:檢查其是否存在波浪度、皺紋、縮孔、夾渣、粘砂、折疊、漏焊、重皮、腐蝕、尖銳劃痕、凹坑(不得超過1.5mm)、凹陷(不得超過管子周長的5%且不大于40mm)等缺陷。
5)每爐批號抽檢一件萬能材料試驗機進行力學(xué)性能復(fù)檢;
6)每爐批號抽檢一件用快速分析檢測材料化學(xué)成分;
7)根據(jù)ASTM 美國試驗及材料協(xié)會的要求對所有來料原材料進行100% UT無損探傷,以確保原材料無裂紋、無夾層。
8)逐件進行硬度檢測:任何一點的硬度應(yīng)符合相應(yīng)標(biāo)準(zhǔn)要求。
9)所有材料的檢驗結(jié)果應(yīng)與原材料的質(zhì)量證明書相對應(yīng);無標(biāo)記、無批號、無質(zhì)量證明書或質(zhì)量證明書項目不全的材料不能使用。
2.1.2材料經(jīng)檢測部門檢驗合格后開具檢驗合格通知單允許轉(zhuǎn)入下道工序,并填寫材料復(fù)檢記錄。(詳見高壓管件理化檢驗控制圖、壓力管件材料管理質(zhì)量控制圖)
2.2切割下料
2.2.1材料下料切割前首先由技術(shù)部門根據(jù)產(chǎn)品成形后外形尺寸和加工方式,考慮管件在生產(chǎn)過程中出現(xiàn)的減薄、變形、各種加工損耗等諸多因素選擇有足夠余量的材料。必要時制作樣板,生產(chǎn)部門按樣板要求的尺寸下料。
2.2.2按設(shè)計要求在切割下料時對原材料的外徑、壁厚、材質(zhì)、管號、爐批號及管件坯料流水編號等內(nèi)容做好標(biāo)識移植,標(biāo)識采用低應(yīng)力鋼印和油漆噴涂的方式,并在生產(chǎn)作業(yè)工序流程卡上記錄操作內(nèi)容。以保證材料在加工過程中的可追溯性。
2.2.3首件下料后,操作人員進行自檢,并報檢測中心專檢人員進行專檢,檢驗合格后再進行其它件的下料,且每件都進行檢測和記錄。對于下料不合格的產(chǎn)品填寫不合格通知單,在通過技術(shù)部門論證后再決定材料能否進行加工,否則應(yīng)將材料報廢。
2.3成型
5.3.1.管件和的壓制成型工藝過程是重要的過程,
5.3.2.清理胎具內(nèi)雜物,檢查電路、油路、臺車是否正常;油料是否充足,電路是否完好;
5.3.3.成型過程中嚴(yán)格控制成型速度及壓力機采用多次擠壓成型的加工工藝。
2.4 焊接
2.4.1 對于鋼板制對焊管件,焊接工作均由有多年焊接經(jīng)驗的專業(yè)焊工進行焊接,拼根據(jù)要求做合適的焊接工藝評定,對焊縫進行力學(xué)性能試驗,在嚴(yán)格的工藝規(guī)程指導(dǎo)下進行焊接生產(chǎn)。焊接過程采用合格的焊接工藝評定,此工藝評定應(yīng)符合JB4708-2008等相關(guān)標(biāo)準(zhǔn)的規(guī)定,焊工也按此標(biāo)準(zhǔn)考核為合格的焊工。在焊接過程中焊工施焊的項目與其考試合格的項目不符,不能進行焊接。在焊接過程中制質(zhì)量保證工程師對焊接工序的停止點和見證點進行規(guī)定監(jiān)控和測量,保證焊接這一關(guān)鍵過程不出現(xiàn)任何缺陷和問題。
2.4.2 焊接過程嚴(yán)格按公司制訂的《焊接工藝指導(dǎo)卡》進行。首先根據(jù)焊條質(zhì)量證明書的說明對焊條進行烘干,烘干后的焊條放在保溫箱中待用。采用氬弧焊打底手弧焊填充和蓋面,打底時管道內(nèi)部充氬保護,以防過熱氧化。焊接過程控制層間溫度低于200℃。焊接時注意層道間的搭接處用鐵錘或砂輪打磨,并清理焊渣和飛濺。
2.4.3 施焊時不允許用碳鋼材質(zhì)作為地線搭鐵,應(yīng)將地線搭鐵緊固在工件上,禁止點焊緊固。鋼板圈圓時,卷板機應(yīng)用無鐵離子的材料覆蓋扎輥表面。組裝過程中不得使用可能造成鐵離子污染的工具。進行酸洗鈍化時,應(yīng)盡量避免對碳鋼部件的酸洗,無法避免時,碳鋼部件必須預(yù)先做好保護措施。
2.4.4 對于焊制管件應(yīng)進行焊后熱處理,保證焊接接頭具有同母材相近的力學(xué)性能和其它技術(shù)指標(biāo)。
2.4.5焊制管件的焊縫必須進行100%射線檢測,并向貴方提供射線探傷報告。
(詳見焊接質(zhì)量控制流程圖)
2.5熱處理工藝
2.5.1熱處理
A、管件需要按照標(biāo)準(zhǔn)的規(guī)定做正火+回火熱處理。有記錄曲線和熱處理報告并做為交工資料的一部分存入產(chǎn)品檔案。
2.5.2 對于P91管件半成品,嚴(yán)格按照相關(guān)標(biāo)準(zhǔn)中規(guī)定的熱處理制度進行熱處理。
2.5.3 熱處理前首先保證熱處理爐爐膛清潔干凈,爐內(nèi)無油、灰、銹及與處理材料不同的其它金屬。
2.5.4所有經(jīng)熱處理的管件應(yīng)逐件進行硬度檢測,并提供相應(yīng)硬度報告。
2.5.5工件在爐內(nèi)擺放要均勻,全部放在有效加熱區(qū)內(nèi),最小間隔不得小于200mm。
2.5.6加熱設(shè)備為4m*20m*2.5m燃?xì)鉅t。每爐均應(yīng)放置隨爐試件。
2.5.7準(zhǔn)備工作:認(rèn)真檢查設(shè)備、導(dǎo)線、熱電偶等,確認(rèn)設(shè)備正常,連接可靠后,方可開機。
2.5.8溫差控制:每爐次應(yīng)力求各管道內(nèi)外壁溫度均勻,恒溫時在加熱范圍內(nèi)任意兩測點間的溫差應(yīng)低于50℃。
2.5.9測溫點布置:熱電偶的安裝位置,應(yīng)以保證測溫準(zhǔn)確可靠、有代表性的原則。水平管道,測溫點應(yīng)上下對稱布置;分區(qū)控溫時,熱電偶的布置應(yīng)和加熱裝置相適應(yīng)。
2.5.10測溫要求:熱處理的測溫必須準(zhǔn)確可靠,應(yīng)采用自動溫度記錄。所用儀表、熱電偶及其附件,應(yīng)根據(jù)計量的要求進行標(biāo)定和校驗。
2.5.11測溫方式:熱電偶、紅外測溫儀。
2.5.12記錄方式:溫度記錄表和熱處理曲線
焊縫熱處理:采用履帶加熱片加熱的熱處理方式。
所有經(jīng)熱處理的管件應(yīng)逐件進行硬度檢測,并提供相應(yīng)硬度報告。
(詳見熱處理質(zhì)量保證體系圖)
2.6機加工及坡口加工
管件的坡口加工采用機械切削方式進行,我公司擁有各種車床、動力頭等機加工設(shè)備20余臺,可根據(jù)訂單規(guī)定的相關(guān)標(biāo)準(zhǔn)及買方要求加工各種厚壁管個采用的雙V型或單V型坡口及內(nèi)坡口和外坡口,我公司可完全按照標(biāo)準(zhǔn)及技術(shù)要求進行坡口機加工,保證管件在焊接過程中便于操作和焊接。
2.7表面處理
2.7.1碳鋼及合金管件內(nèi)外表面在機加工完成以后用噴砂機對管件的內(nèi)外表面時行噴砂除銹處理,經(jīng)噴砂和打磨后的管件內(nèi)外表面光滑呈現(xiàn)出金屬光澤,管件不允許銹蝕、氧化皮、重皮等不良缺陷存在。
2.8成品管件檢測
2.8.1所有管件均應(yīng)進行外觀檢查。外觀檢查應(yīng)逐件進行,并符合以下要求。對不浸入最小壁厚的結(jié)疤、裂紋、折疊、夾渣等缺陷,允許研磨清除,消除缺陷后剩余壁厚不得小于壁厚。否則,該管件應(yīng)予以報廢。
2.8.2對于管件在出廠前按訂貨要求所對應(yīng)的標(biāo)準(zhǔn)要求或買方指定要求進行各種檢測,各種檢測均由國家技術(shù)監(jiān)督局認(rèn)可的具有相應(yīng)資質(zhì)的專業(yè)人員完成。
2.8.3管件成品進行以下檢測
1)所有管件均應(yīng)按指定相關(guān)標(biāo)準(zhǔn)要求做幾何尺寸檢測。檢測項目允許的偏差符合相關(guān)標(biāo)準(zhǔn)。
2)所有碳鋼及合金管件,應(yīng)逐件進行100%MT檢驗,對于MT檢測出的深度不大于0.8mm的微裂紋,允許研磨清除。否則,該管件予以報廢。
3)所有管件的焊接坡口,均應(yīng)進行100%MT或100%PT檢驗,檢驗執(zhí)行JB/T4730-2005
2.8.4向用戶提供管件各種無損檢測報告(金相組織、熱處理報告、UT等)、幾何尺寸檢驗記錄和產(chǎn)品質(zhì)量證明書。